Streamlining after-sales service with asset management function
Asset Management
ServAir’s asset management function manages products delivered to customers in a hierarchical structure. The management of repair history, replacement parts history, and maintenance plans can be done in association with asset information, allowing you to check the latest asset information. You can respond to customers quickly and optimally by using this asset information whenever necessary for business.
Sharing the latest asset information (Service BOM)throughout the company
In after-sales service, parts that comprise a product are typically managed in units called Service BOMs, which are units used in repair service. ServAir allows asset management in a hierarchical structure, such as parts A & B that comprise a product and parts C & D that comprise part B. If part C is replaced during repair work, by registering the replaced part as C, the call center can respond while checking when, by whom, and for what repair the replacement was performed.
In addition, regular data updates/maintenance are essential in asset management as asset information must always be up-to-date. If parts that comprise asset change during repair, ServAir can automatically reflect these changes in repair result. This prevents any omissions in the system and allows sharing of the latest asset information among all parties involved.
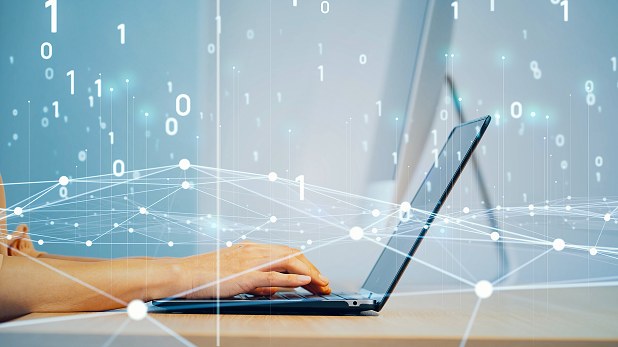
The asset information and maintenance plans/preventive maintenance
The asset management can also be helpful for maintenance planning. The asset management supports the formulation of optimal maintenance plans at that time, as you can check asset information such as the latest status of delivery dates, repair history, and parts replaced during repair. You can propose work plans to customers based on a devised maintenance plan, which results in the realization of “preventive maintenance” that reduces the probability of sudden failures as much as possible.
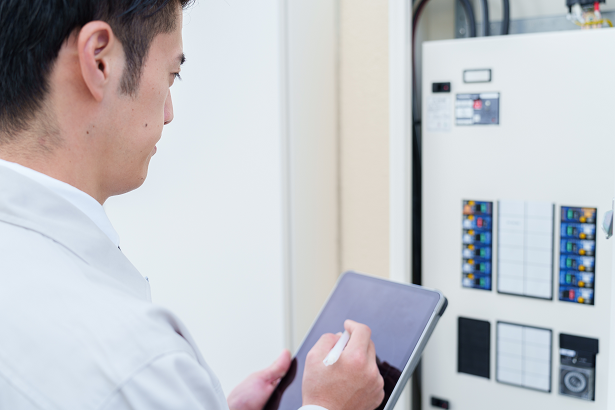
Other Functions
Customers
-
Introduced ServAir as a field service platform that can flexibly respond to company policies and aims to leverage it along with IoT to link to preventive maintenance.
-
Introduced ServAir, an all-in-one package that includes core business operations, and achieved a 60% reduction in overtime despite a 20% increase in sales processing.
-
Realize DX of calibration work process by centralized management of work managed by multiple systems centered on ServAir.
-
Realized ‘Global One Service Management Platform’ used by 6,000 service engineers from 80 countries at 230 service bases around the world.