Supports periodic inspection
in after-sales service
Periodic Inspection
ServAir allows managing periodic inspection plans and work results together. The periodic inspection in after-sales service is planned and coordinated in advance, ensuring that it will not interfere with the customer’s daily operations. In addition, it is also necessary to ensure that periodic inspection services are provided in accordance with the scheduled periodic inspection dates and ServAir supports these tasks efficiently.
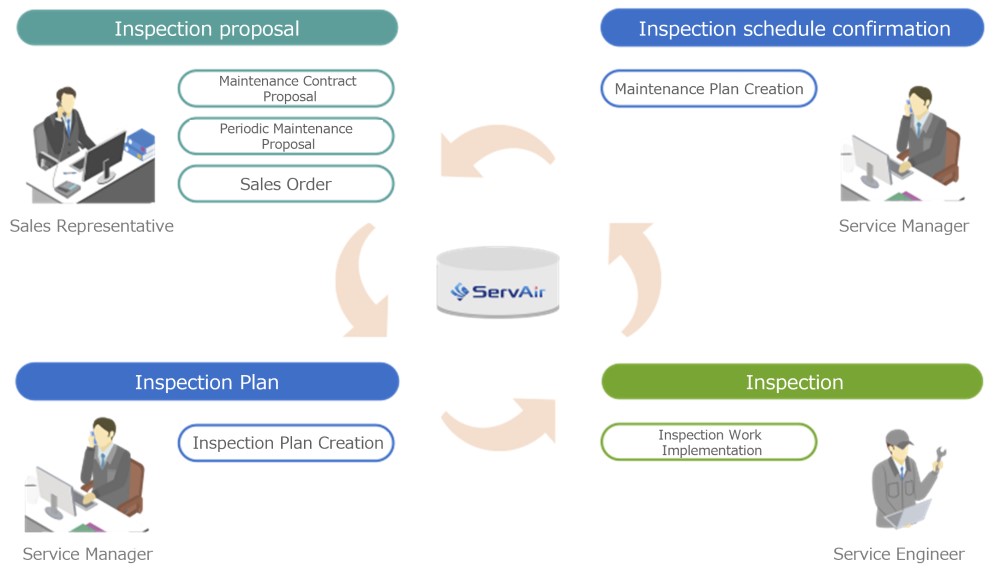
Efficient support for periodic inspection operations
-
Confirmation of periodic inspection schedule
You can confirm periodic inspection and maintenance plans in chart form as a schedule. You can visually check periodic work plans for target customers in an easy-to-understand format, streamlining the time-consuming coordination process with customers. It is also easy to confirm that the periodic inspection work is being performed on the scheduled periodic inspection date and without omissions.
-
-
Creation of periodic inspection plan
By regularly checking the operating status of products at periodic intervals, you can detect signs of problems before they occur.
ServAir can automatically manage the next periodic inspection after the periodic inspection work has been carried out. This allows creating your next work plan and take action without missing anything. -
Allows creation of appropriate maintenance plan
Maintenance is carried out with the aim of not only ensuring that products operate without failure but also maintaining them in the most efficient operating condition.
To do this, it requires an accurate understanding of the condition of the products installed at the customer’s site. ServAir manages information on products installed at the customer’s site as assets, making it easy to determine which customer installed the product requiring maintenance, when it was installed, and what kind of repairs or parts replacements were performed, which allows creation of a maintenance plan that is appropriate according to the condition.
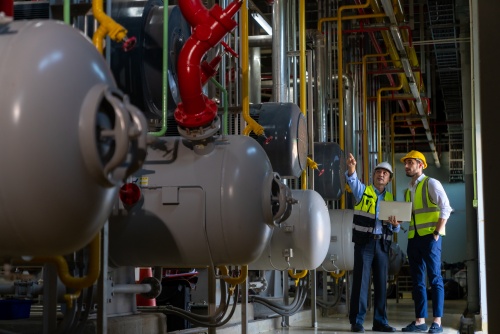
Other Functions
Customers
-
Introduced ServAir as a field service platform that can flexibly respond to company policies and aims to leverage it along with IoT to link to preventive maintenance.
-
Introduced ServAir, an all-in-one package that includes core business operations, and achieved a 60% reduction in overtime despite a 20% increase in sales processing.
-
Realize DX of calibration work process by centralized management of work managed by multiple systems centered on ServAir.
-
Realized ‘Global One Service Management Platform’ used by 6,000 service engineers from 80 countries at 230 service bases around the world.